Le Look 795 : L'ingénierie et la conception Française !
En cette saison 2016, nous avons choisi de faire un essai longue durée du Look 795 Aerolight dans les mains de notre champion du monde master 2014, Jean-Luc Chavanon. Première étape, nous sommes donc allés suivre les processus de conception et fabrication de celui-ci au cœur des usines de cadres Look !
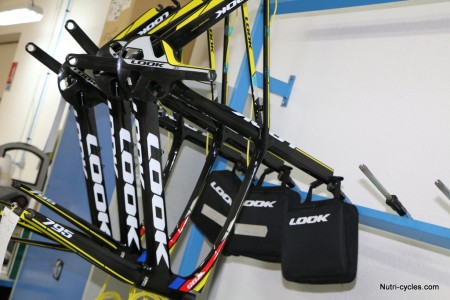
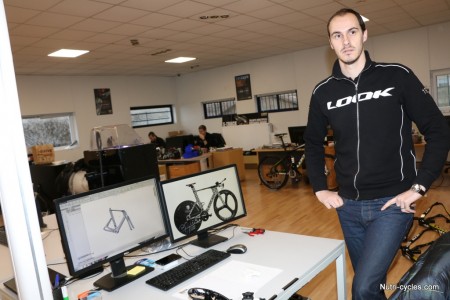
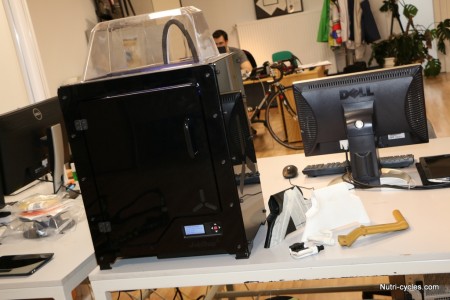
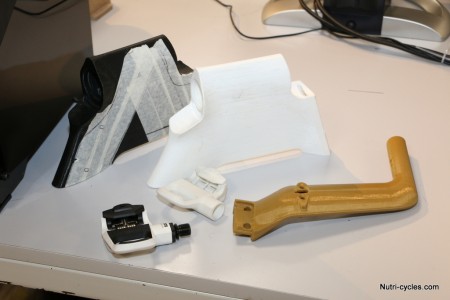
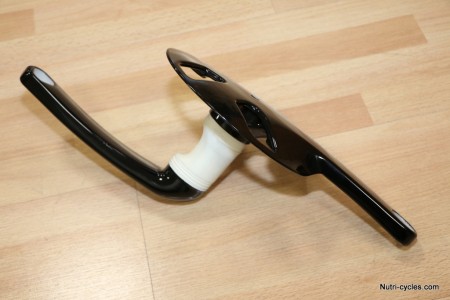
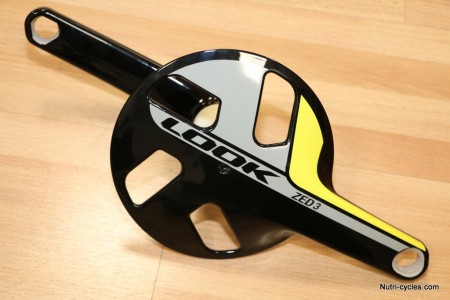
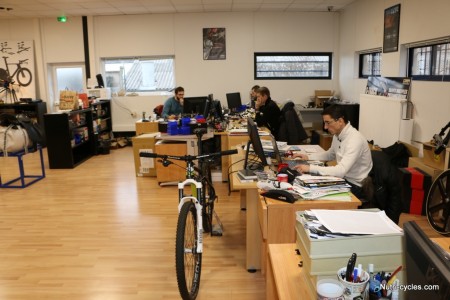
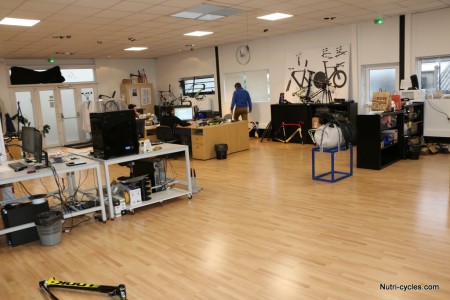
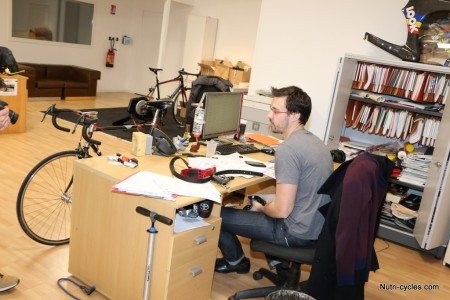
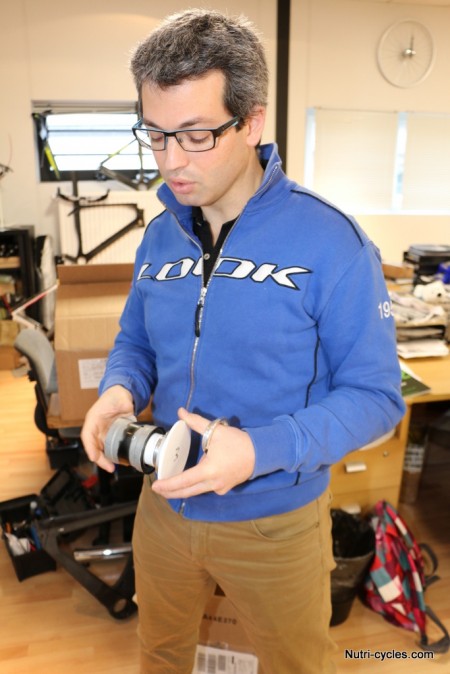
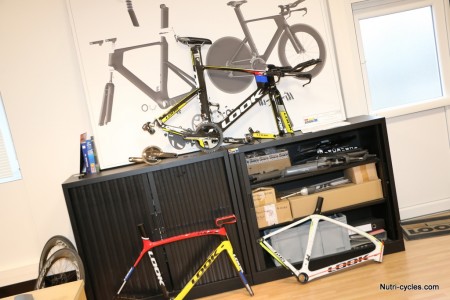
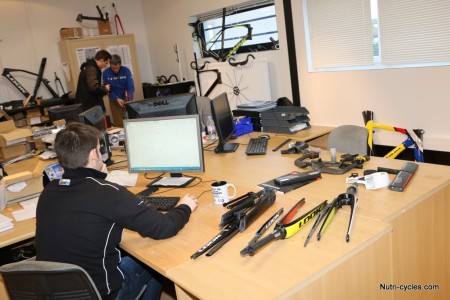
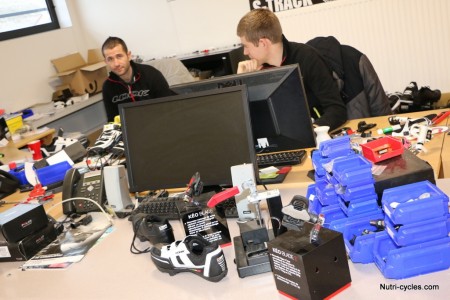
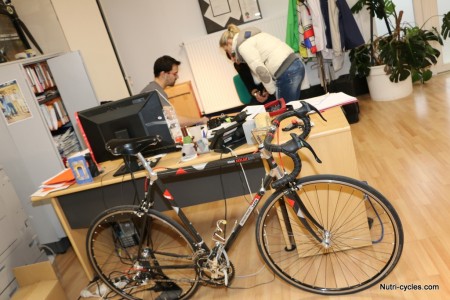
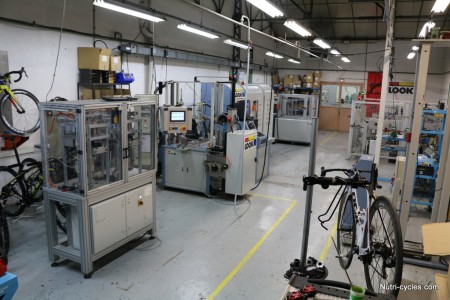
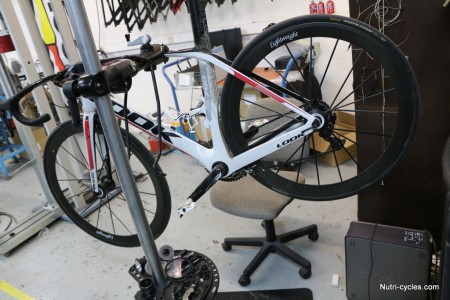
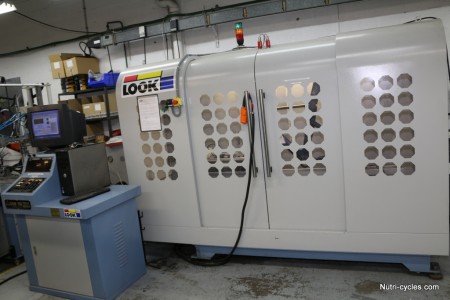
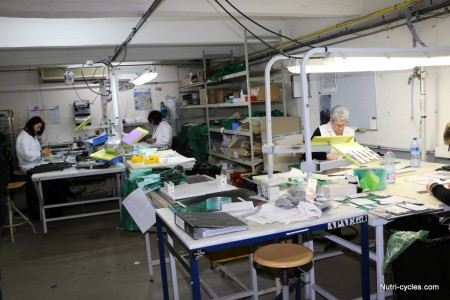
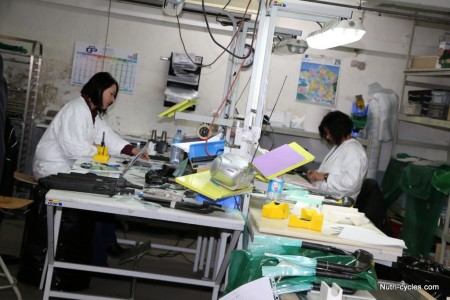
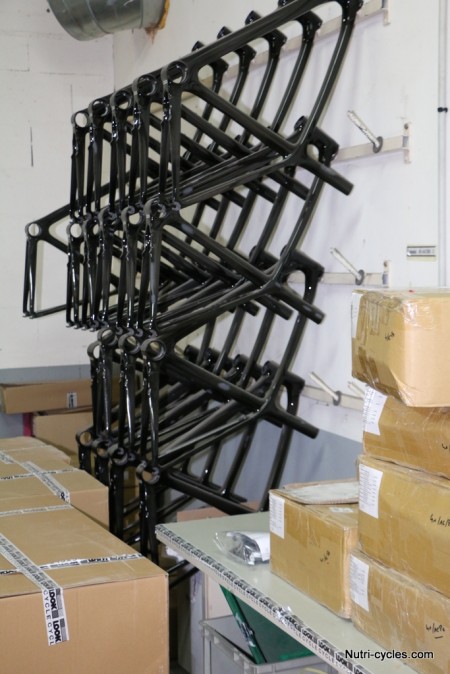
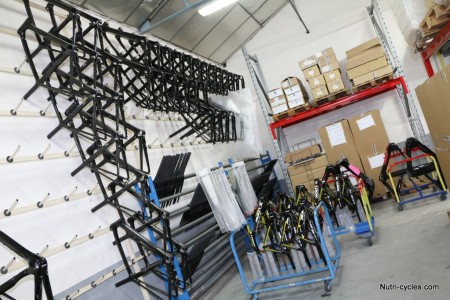
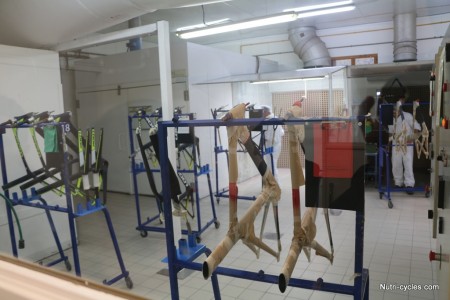
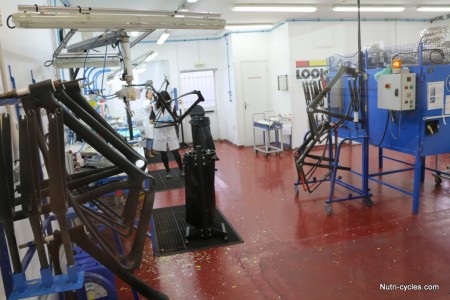
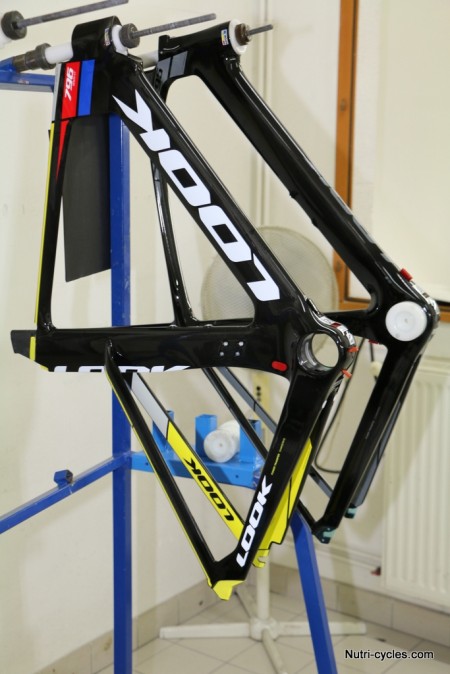
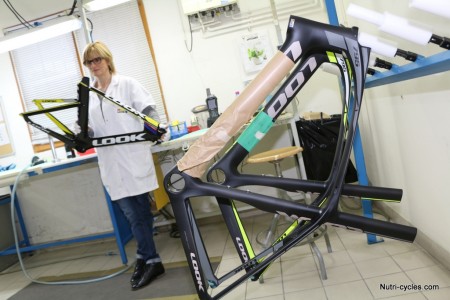
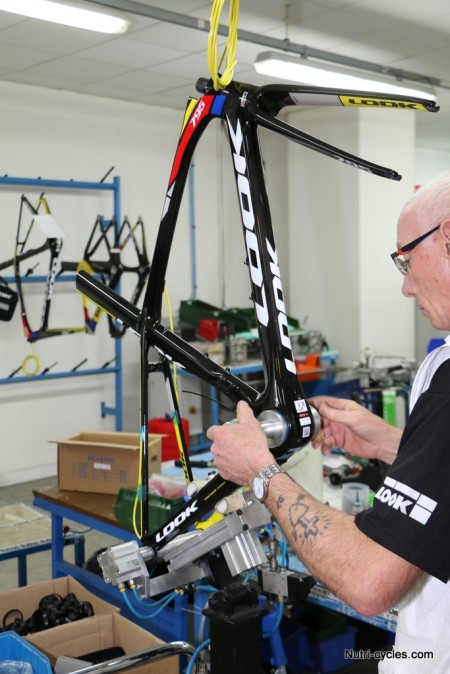
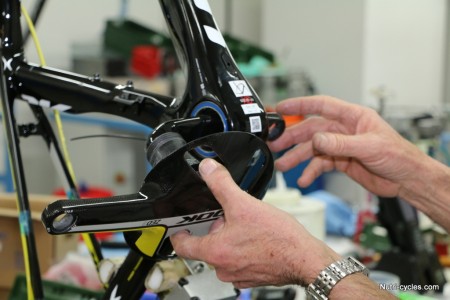
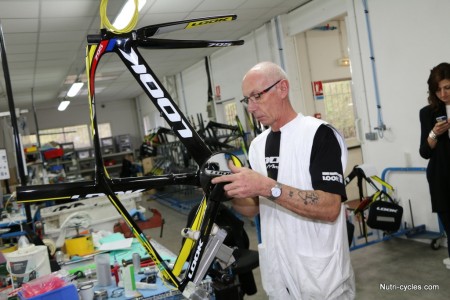
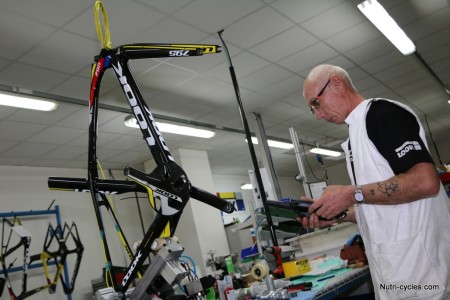
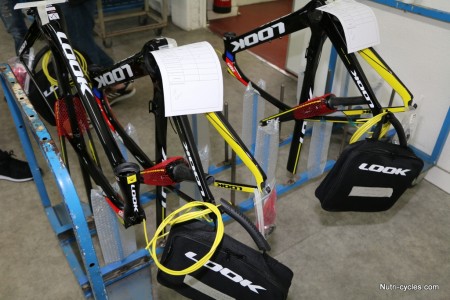
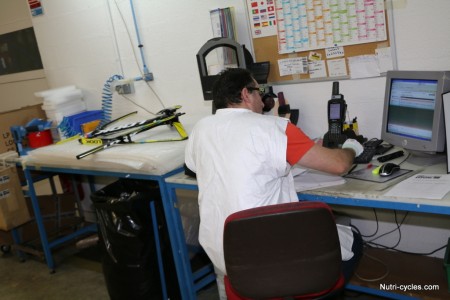
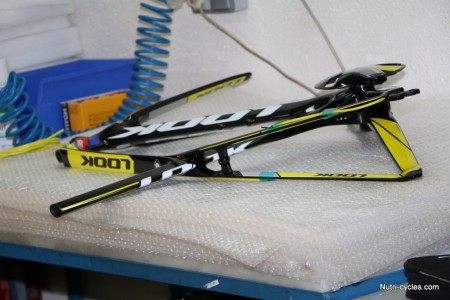
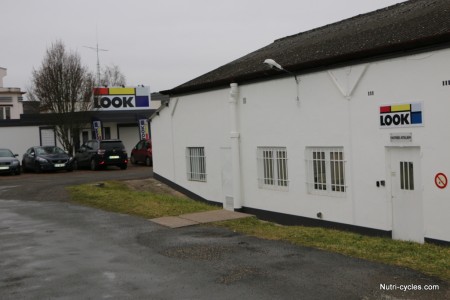
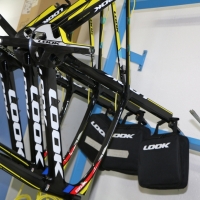
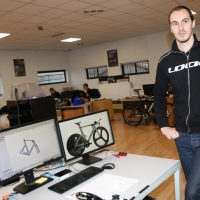
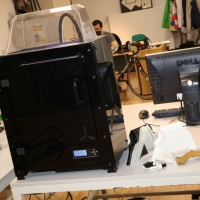
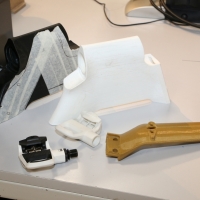
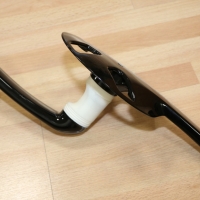
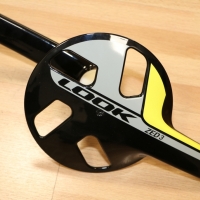
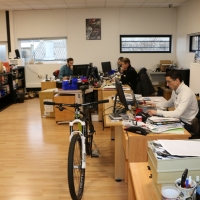
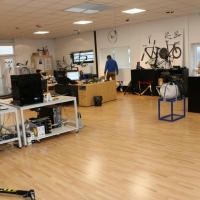
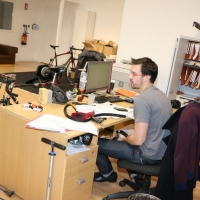
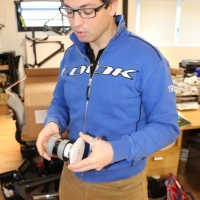

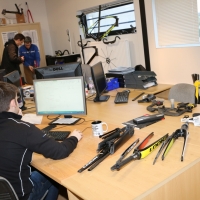
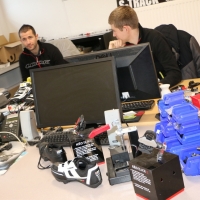
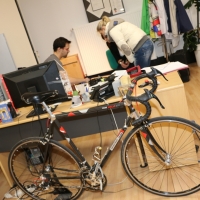
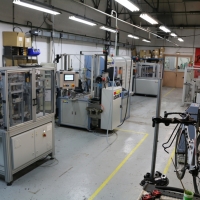
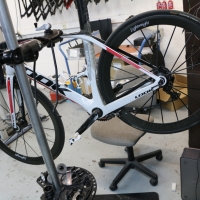
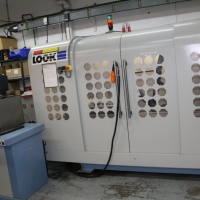
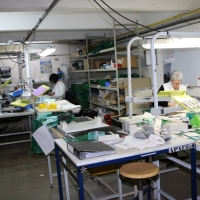
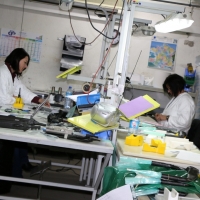
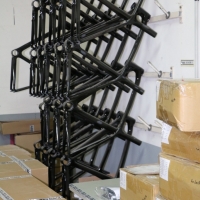
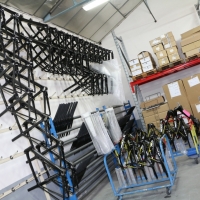
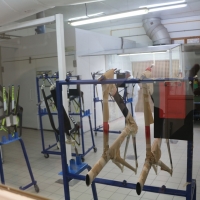
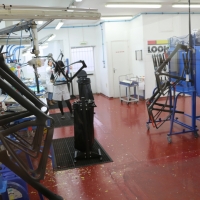
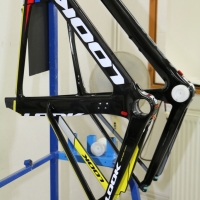
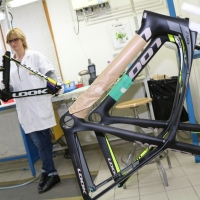
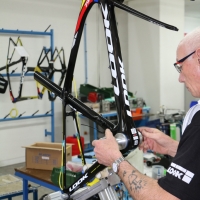
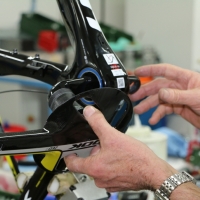
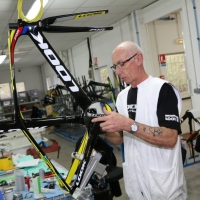
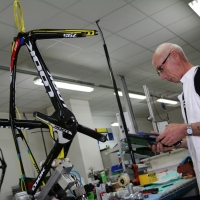
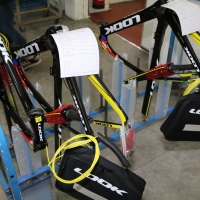
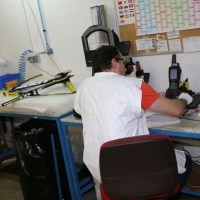
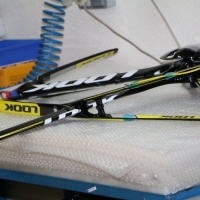
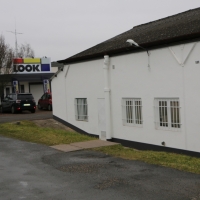
Nous allons suivre précisément le processus de conception du Look 795, mais d'autres cadres de la firme suivent la même logique. Tout d’abord pour bien comprendre les processus mis en œuvre par Look pour assumer sa production de cadres, il faut savoir que le constructeur Nivernais utilise trois principaux lieux dans le monde pour concevoir et produire ses cadres de vélo (Informations données pour la route exclusivement).
France |
Tunisie |
Asie |
---|---|---|
Usine Look |
Usine Look |
Sous-traitant |
Bureau d’études, d'ingénierie et prototypage |
Réception plans et mise en production |
Réception plans et mise en production |
Conception des cadres |
Fabrication des cadres et accessoires des modèles : 695 |
Fabrication des cadres et accessoires des modèles : 675 |
Décoration |
Décoration |
Décoration |
Outils de tests et analyses globales |
Outils de tests et analyses de la production |
Outils de tests et analyses de la production |
Conception/entretien des outils de production |
Conception/entretien des outils de production |
NC |
150 personnes |
170 personnes |
NC |
Tout commence à Nevers !
Toute la conception est réalisée à Nevers, que ce soit au niveau des cadres, des périphériques innovant propres à Look (Potence AeroStem, tige de selle Ergopost, tige de selle pédalier ZED, pédales Look Kéo Blade 2) Ici une équipe d’ingénieurs travaille sur la conception et le prototypage des futurs modèles de pièces et cadres. Dans ces bureaux, l’ensemble des pièces sont tout d’abord conçues via un logiciel de modélisation. Les ingénieurs travaillent ici à la conception, réalisation, mais également aux différentes simulations de pénétration dans l’air, simulation des torsions en application à différentes forces, …
La grande nouveauté depuis quelques années est la possibilité de concevoir les petites et moyennes pièces très facilement via l’impression 3D plastique. L’intérêt est important car il permet de supprimer une phase de production réelle en carbone et donc de limiter les coûts.
Comment sont imaginés les modèles de vélos de demain ?
Marketing, aérodynamisme, étude de la concurrence, ici les ingénieurs s’affairent à imaginer les cadres et accessoires sur lesquels vous roulerez demain. Alors lorsqu’on est une marque innovante en matière de création, on ne chôme pas. Aérodynamisme, légèreté, étude de marché, idées innovantes, améliorations, … C’est un assemblage de toutes ces notions qui font le futur cadre sur lequel les ingénieurs vous ferons rouler !
Quels sont les composants d’un cadre carbone ?
La fibre carbone vient du pétrole. On fabrique du nylon puis du polyacrylonitrile avec lequel on fait de la fibre de carbone. Dans la filière carbone, on caractérise les matériaux selon les critères suivants :
- Isotropes : Présentant les mêmes caractéristiques physiques dans toutes les directions
- Anisotropes : Présentant différentes caractéristiques selon son orientation
Pour exemple, voici les différentes densités liées à deux matériaux bien connus des fabricants :
- Densité aluminium 2,7 grammes/cm3
- Carbone 1,75 grammes/cm3
Trois types de fibres composent un cadre de vélo :
- Fibre HR : Haute Résistance
- Fibre HM : Haut Module
- Fibre IM : Module Intermédiaire
L’épaisseur d’une fibre mesure entre 4,5 et 7,5 microns (Epaisseur d’un cheveu 50 à 100 microns). Les fabricants mondiaux de carbone sont Toray, Toho et Mitsubishi. Les nappes de carbone arrivent directement composées avec de la colle qui aura ensuite un comportement précis lors de la cuisson en fonction de la température. C’est ici différent de la technologie RTM de Time, on tisse et on injecte l’époxy (Moins de maitrise sur le poids).
Avec toutes ces informations, on a deux conditions désormais pour le comportement d’un cadre : Le couple fibre HM et HR en appliquant le croisement optimal des fibres (droites, croisées). Afin de fabriquer la pièce il va falloir draper les couches de fibres précisément. LDS utilise des nappes qui vont de 110 (unidirectionnelle) à 230 grammes (Tafta), avec un taux de résine de 35 à 38%. On obtient ainsi une multitude de pièces à assembler.
Méthodes de création des pièces et drapage du carbone
Les ingénieurs conçoivent la méthode d’assemblage des pièces de feuilles carbone à constituer pour monter/fabriquer le cadre. Ici une équipe d’assembleuses intervient afin de mettre en application le processus sur des moules, eux aussi conçus par les ingénieurs.
Pour information, ce sont plus de 400 pièces de feuilles de carbone qui composent un cadre complet. Chaque pièce a son rôle. Pour exemple précis dans le cas du Look 795, un triangle avant contient 138 pièces, la fourche 41 pièces. Cette méthode, c'est le drapage.
Conception des moules et cuisson des pièces carbone
Pour une bonne compréhension des termes utilisés, vous pouvez vous reporter à notre dossier : Les composants d'un vélo de route
On va ensuite concevoir les moules (C’est Look qui conçoit ses propres machines, faisant ensuite sous-traiter à un spécialiste la fabrication) qui serviront à chauffer les pièces du cadre afin qu’il entre dans sa phase rigide, et produire ainsi les premières séries de pièces, les poncer, les assembler, ...
A lire : Visite usine de cadres de vélo Look en Tunisie
Les ingénieurs du constructeur Nivernais peuvent ainsi palper les premiers prototypes afin de vérifier sa conformité par rapport au cahier des charges (informations logicielles). C’est un gain de temps considérable ! Les ingénieurs utilisent des machines de test pour jauger des échantillons prélevés afin de s’assurer de la qualité de la production (normes respectées et fiabilité du produit).
Décoration et peinture : Aux petits oignons !
Les étapes de peintures sont longues et fastidieuses. Jusqu’à 4/5 couches de peinture peuvent recouvrir un cadre avec des processus de finition (ponçage, bouchage des petits trous, aspérités, décorations, vernis, polish, …) très longs. Un cadre peut ainsi repasser plusieurs fois entre les mains d’une même personne après un processus afin qu’il soit à nouveau vérifié pour finir parfait.
Une usine en Tunisie
Implantée historiquement en France à Nevers, avec les fabrications des KG66, KG96 pour exemple, la société LDS (Look Design Concept) voit le jour en Tunisie en 2001. C’est une filiale de Look cycle Internationale conçue pour répondre à différentes contraintes dont celle principale de baisse des coûts. Car vous allez le voir dans nos reportages, fabriquer et peindre un cadre révèle une grosse quantité de travail manuel qualifié. La baisse des coûts pour pérenniser/sauver l’entreprise certes, mais pas que !
Les avantages à produire en Tunisie sont multiples : Distance très proche de la France (Aller-retour conception et expéditions rapides), la langue est le Français (facilité de la formation des ouvriers qualifiés), système comptable proche, droit du travail assez proche, pas de fuite de la technologie (on limite la contrefaçon), maitrise de l’ensemble de la filière, …
Une fois le processus de production finalisé et validé en France, il va être reproduit à plus grande échelle en Tunisie (Look 695, 795 et 796). Les matières premières utilisées sont également analysées ici. Elles sont achetées par la France, mais en revanche, elles seront livrées directement en grosse quantité en Tunisie pour la production. Fabrication et peinture seront réalisés (695, 795 et 796) en Tunisie mis à part quelques modèles liés au configurateur personnalisé du site Internet Look. Ceux-ci vont être intégralement poncés et peints en France. Pour les cadres milieu de gamme (675 et 765) ceux-ci sont produits en Asie.
La firme emploie 170 ouvriers qualifiés en Tunisie, avec également des profils de formateurs afin de maintenir le niveau de qualité de production. Les cadres et pièces une fois produits et peints en Tunisie seront ensuite livrés ici à Nevers afin d’être assemblés et montés avec les groupes, périphériques et roues.
L'assemblage final du vélo
C’est une affaire de savoir-faire de montage qui est réalisé intégralement à la main par les ouvriers Français. Câbles et gaines, jeu de direction, cintre et potence, groupe Shimano ou SRAM, montage du pédalier, des pédales, … Les mains expertes des assembleurs opèrent avec une précision et une expérience.
Pour exemple, un 795 Aérolight qui voit ses passages de gaines intégrées au cintre et potence nécessite une procédure précise afin de fonctionner sans frottements ou points durs. Les vélos sont ensuite emballés et prêt à être expédiés au revendeur.
Look un fabricant de cadre devenant un fabricant de vélos !
On assiste véritablement à une évolution du métier de la firme Nivernaise. Acteur majeur dans la fabrication de pédales automatiques, Look souhaite désormais passer du stade de constructeur de cadre à constructeur de vélos complets. Potence AeroStem, tige de selle Ergopost, tige de selle pédalier ZED, pédales Look Kéo Blade 2 et plus récemment freins intégrés sur les versions 695 Aerolight et 795 Aerolight. Pensons également au Look 796 disponible en version Triathlon ou CLM.
Pour preuve cette année le modèle Look 765 qui en version Shimano 105 se taille une place intéressante dans les vélos haut de gamme. Look a désormais pensé ce modèle en version complète. En optimisant les composants qui équipent le vélo afin de maintenir un prix global bien placé.
A lire : Look 765 : La nouvelle ligne endurance du constructeur Français !
Plus récemment, la société Nivernaise Look à annoncé une prise de participation majoritaire au sein de la PME française spécialisée dans la conception et la fabrication de roues carbone, Corima.
Vélo et cadre : Où acheter ?
>> Vous pouvez commander votre matériel ou équipement chez notre partenaire
Découvrir Look Cycle : Cadres carbone et pédales automatiques
>> Toutes les informations sur Look Cycle : Cadres carbone et pédales automatiques